Customizable Motor Laminations
At YUANZHONG, our motor laminations can be customised to meet your unique specifications. We use state-of-the-art Japanese equipment and Baosteel material to ensure exceptional magnetic conductivity and reduced iron loss, resulting in motor cores that are both durable and precise in speed control. Our high-speed punching machines and tungsten steel molds with precise guide pillars allow for the production of stator cores with varying features. With our commitment to high production efficiency and stable mold production, we guarantee flawless outcomes tailored to your specific needs.
YUYAO YUANZHONG
MOTOR PUNCHING CO., LTD
No.28, Gansha Road,
Lubu Town, Yuyao City,
Ningbo, Zhejiang,
China
E-mail yuanzhong@yuanzhong.cn
CDZ Gmbh
Dieselstr. 42,
D-41352 Korschenbroich,
Germany
E-mail info@cdz-gmbh.com
WEB www.cdz-gmbh.com

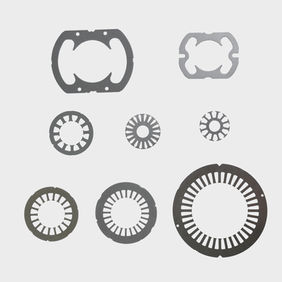

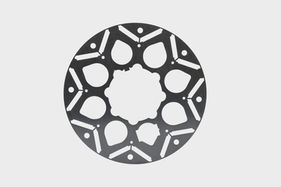

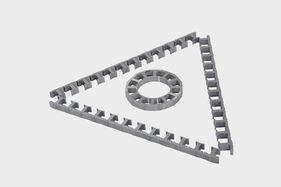
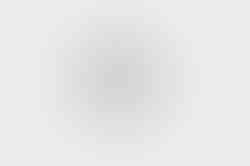



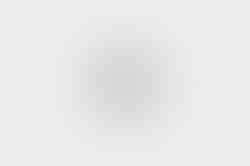



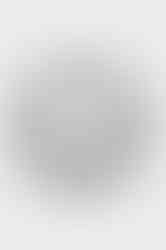



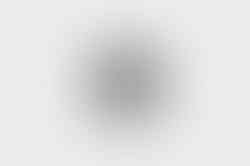




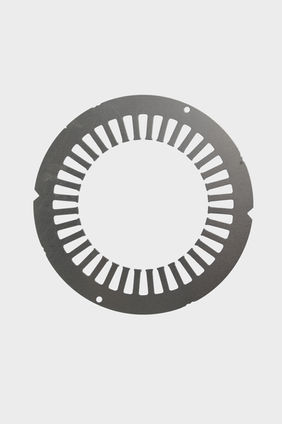







-
What certifications do you hold?Our processes are certified according to IATF 16949:2016, ensuring high standards in quality management for the automotive industry and other high-precision sectors.
-
What are your payment terms?For orders ≤ 1000 USD, we require 100% payment in advance. For orders ≥ 1000 USD, we require 50% payment in advance and the remaining balance before shipment.
-
Can you provide one-stop services for motor core laminations?Yes, we offer comprehensive one-stop services for motor core laminations, from prototypes to series production. This includes additional services like aluminum casting, injection molding, winding, and magnetic steel integration.
-
How do I get started with a project?Simply fill out the "Request a Quote" form on our website. Our team will review your requirements and contact you to discuss possible plans and options to meet your needs. We're here to support you every step of the way.
-
What materials do you use for motor core laminations?We primarily use cold-rolled non-oriented silicon steel for our motor core laminations. This steel is chosen for its high thermal conductivity, excellent electrical insulation properties, and low magnetic losses. We also offer the flexibility to meet special material requirements through our close collaborations with steel mills.
-
What is the minimum material thickness you can stamp?We can stamp materials with a minimum thickness of 0.2mm, maintaining a high precision with a minimum tolerance of 0.02mm.
-
What stamping techniques do you offer, and what are their differences?We offer three main stamping techniques: compound stamping, high-speed progressive stamping, and interlock progressive stamping. Compound Stamping: Best for low to medium-volume production, balancing time efficiency and cost. Material loss is moderate. High-Speed Progressive Stamping: Ideal for high-volume production with significant time efficiency and lower material loss, but initial tooling costs can be higher. Interlock Progressive Stamping: Optimized for complex designs with excellent material efficiency, though it may require more time and investment upfront. If you have specific needs, feel free to contact us by filling out the "Request a Quote" form, and our team will help determine the best option for your project.
-
What are the benefits of using glue bonding techniques in motor lamination stamping?Glue bonding techniques in motor lamination stamping offer several advantages: Reduced Material Loss: Glue bonding minimizes the need for additional fastening materials like rivets or welds, leading to less material waste. Enhanced Structural Integrity: The bonding process creates a uniform and stable structure, reducing the risk of delamination or vibration during motor operation. Improved Efficiency: Glue-bonded laminations have better magnetic properties due to reduced air gaps, which enhances motor performance. Cost-Effective: By eliminating the need for extra materials and reducing assembly time, self-bonding can lower overall production costs.
