Our Capabilities
Our Facility
Yuanzhong has a state-of-the-art manufacturing facility that enables us to produce high-quality motor punching pieces and motor iron cores for a wide range of applications. Our plant covers an area of 20,000 square meters and is strategically located in Ningbo, Zhejiang, with easy access to transportation.
Machinery
We have a range of advanced machines, including:
-
11 high-speed stamping presses ranging from 25 to 300 tons (including brands such as Fuchuan FHD, AIDA from Japan, and INGYU from Taiwan)
-
20 general stamping presses ranging from 16 to 250 tons
-
6 aluminum die-casting machines ranging from 45 to 280 tons
-
1 Panasonic industrial robot welding machine
-
2 projectors for inspection
Production Capacity
Our monthly production capacity is approximately 800 tons of electrical steel (silicon steel) for motor punching pieces.
Moulds
We currently have 150 sets of moulds available for production.
Material
Main Markets
Our facility serves customers both domestically and internationally,
with the following breakdown:
-
China: 39%
-
Europe (Germany, Spain, Italy, Switzerland): 40%
-
Japan: 15%
-
Other: 6%
We take great pride in our facility and are committed to continuously investing in new technologies and processes to improve our manufacturing capabilities.
Factory Tour
Our Advanced Manufacturing Techniques
Self-bonding, or glue-bonding, is an innovative technique that uses specialized adhesives to create seamless, robust connections between materials. This method minimizes material loss and assembly time, making production more cost-effective. With the ability to accommodate complex designs, self-bonding enhances structural integrity while providing a cleaner aesthetic finish by eliminating traditional fasteners. Versatile across various materials, it is ideal for industries like automotive, industrial, and renewable energy, promoting efficiency and innovation in manufacturing.
Self-Bonding
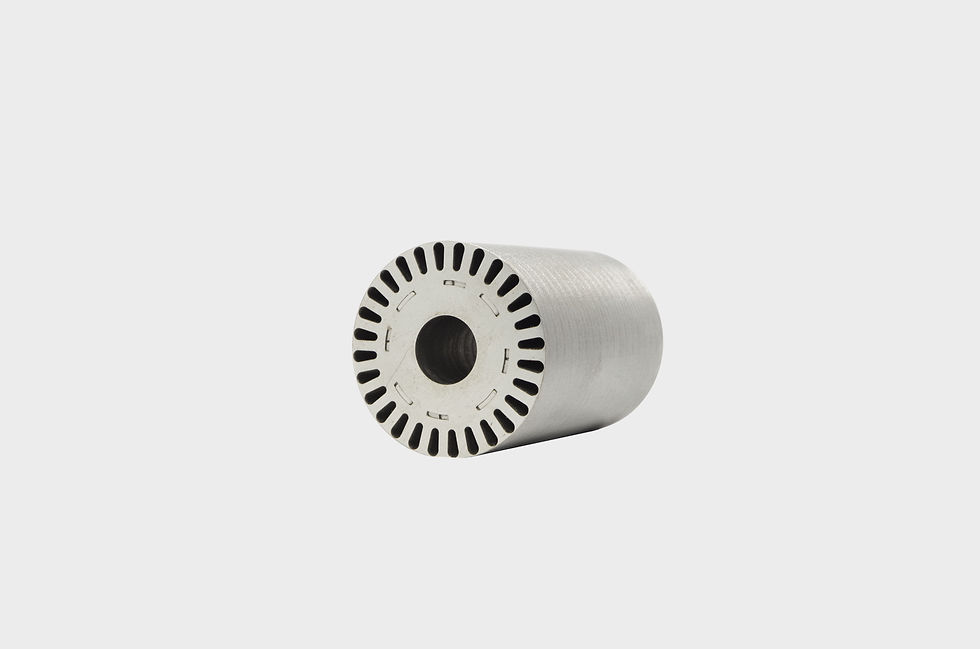
Laser cutting is a precise and versatile manufacturing technique that uses a focused laser beam to cut materials accurately. Known for its speed and ability to handle intricate designs, laser cutting is ideal for both prototyping and mass production. Its non-contact process ensures minimal material deformation while delivering clean edges and smooth finishes. Additionally, laser cutting can work with a wide range of materials, including metals and plastics, making it a flexible solution. Key advantages include fast production, reduced material waste, and the ability to meet complex, design-oriented requirements, making it a popular choice across industries.
Laser Cutting

Self-locking techniques provide a reliable and efficient way to bond motor laminations without traditional fasteners or adhesives. This method enhances structural integrity, speeds up production, and reduces material costs. It also allows for greater design flexibility, enabling more complex geometries, while improving resistance to vibrations and thermal stresses. Overall, self-locking offers a cost-effective and durable solution for motor lamination bonding in industries like automotive and renewable energy.
Self-Locking

YUYAO YUANZHONG
MOTOR PUNCHING CO., LTD
No.28, Gansha Road,
Lubu Town, Yuyao City,
Ningbo, Zhejiang,
China
E-mail yuanzhong@yuanzhong.cn
CDZ Gmbh
Dieselstr. 42,
D-41352 Korschenbroich,
Germany
E-mail info@cdz-gmbh.com
WEB www.cdz-gmbh.com
